Global electricity demand is rising, with the world’s energy watchdog, the International Energy Agency, predicting growth by an average of 3.4% annually through 2026. Whilst this can boost economic growth, increased energy production accelerates the consumption of fuel resources faster than nature can feasibly replenish them, harming the environment and leaving energy-intensive industrial sectors vulnerable to price shocks.
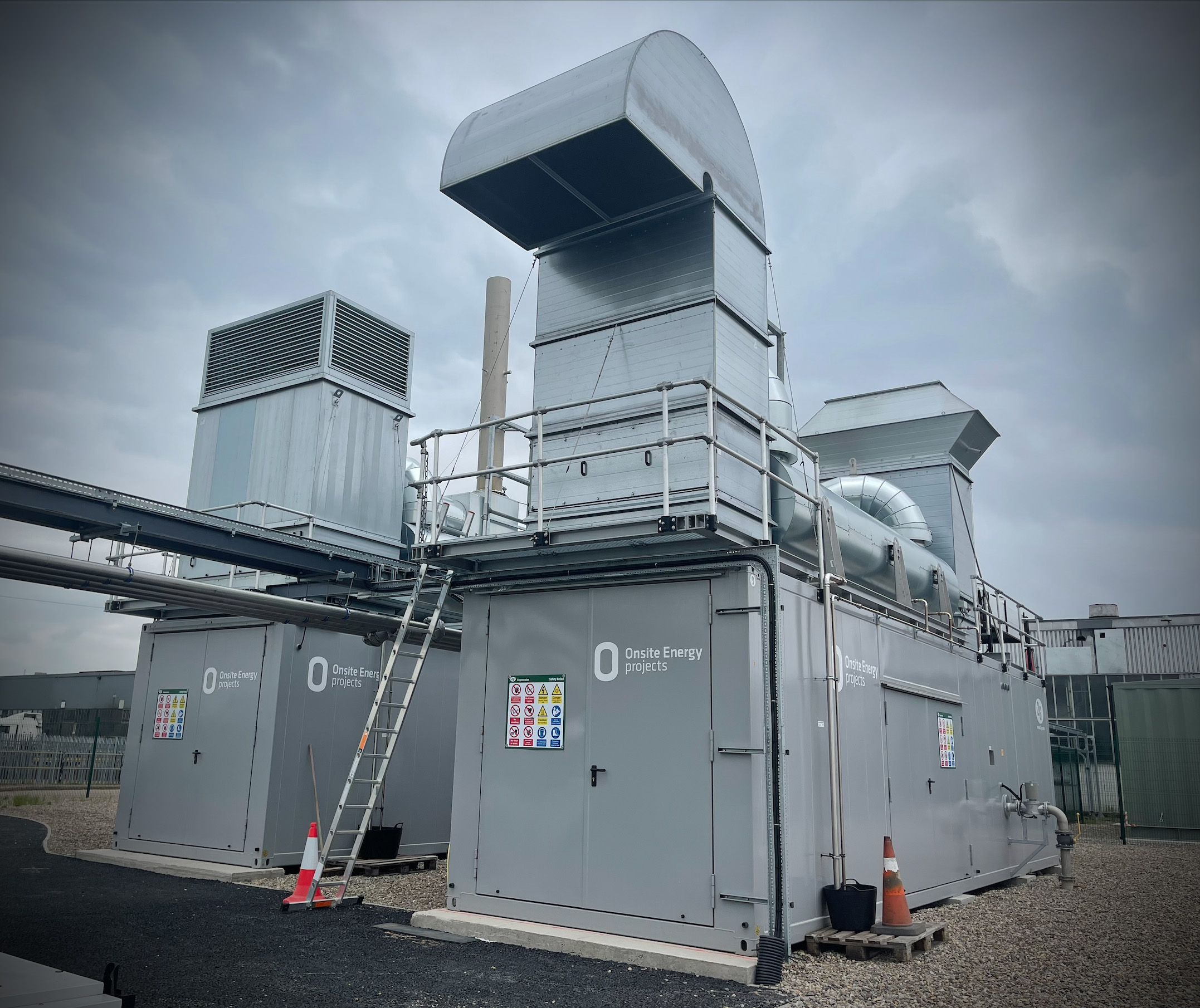
On-Site Energy CHP System
On-Site Energy, a leading provider of low-carbon and renewable energy centres for manufacturers, build combined heat and power (CHP) systems on-site, to help their clients reduce energy costs, lower carbon footprints, and take control of their own energy supplies to ensure their operations are more sustainable.
CHP systems produce electrical and thermal energy closer to the point of consumption, allowing the excess thermal energy to be used for heating buildings or within industrial processes. This method of energy generation is both more carbon efficient and more cost-effective than buying power from the grid as it produces the required heat on-site, freeing users from reliance on the grid and any related issues and constraints.
With a growing portfolio of clients, including a large, global automobile manufacturer, On-Site Energy looked to Intelligent Industries, a leading end-to-end industrial IoT provider, to create a bespoke solution that would enable remote monitoring and control of their CHP systems across different manufacturing sites.
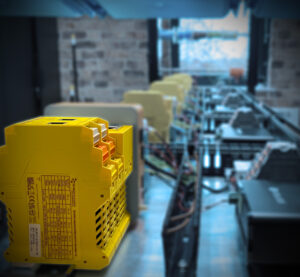
Intelligent Industries CHP remote monitoring system for On-Site Energy
Using Brainboxes Remote IO and industrial Ethernet switches, Intelligent Industries built a standardised industrial control panel for the on-site energy centres with a cloud-based platform providing dashboards, reporting and alerting.
Designed for demanding environments, the Brainboxes within the smart system enabled Intelligent Industries to monitor signals from a variety of sources, including electricity meters, gas meters and G100 devices.
G100 is an Energy Networks Association (ENA) and National Grid regulation that defines limits on energy installations. By monitoring the overall current flow at the installation’s exit point, G100 devices are crucial to understanding on-site demand and ensuring the agreed Export Capacity is never surpassed. Intelligent Industries’ smart system uses Brainboxes robust analog IO modules to receive signals from the G100 devices, ensuring on-site generation remains compliant, avoiding shutdowns and fines, and making the system key to effective energy generation and management.
Alongside the Ethernet to Analog devices, industrial Ethernet to Digital IO Brainboxes capture pulse signals from gas meters, enabling consumption to be further measured and tracked. Using digital signals, the Remote IO devices detect faults in external equipment and monitor the status of the pump room. A Linux based edge computer, running Azure IoT Edge and custom Azure IoT Edge modules utilising the Brainboxes SDK, continually monitor the IO telemetry, which is then sent to Azure IoT Hub, Microsoft Azure’s cloud-based IoT service, for further processing and analysis within the cloud.
“When there’s an issue in that pump room, the digital signals from Brainboxes ED-588 will trigger and tell us there’s an issue, and we can action it and alert the site in real-time. Then they can go in straight away and investigate the issue.”
– James Brand, Director at Intelligent Industries
Intelligent Industries created a full IoT and data platform architecture within Microsoft Azure, creating Digital Twins allowed Intelligent Industries to define an ontology that represents the energy centre, with real-time updates applied to the twins, while Azure Data Explorer provides a scalable data historian, enabling advanced reporting scenarios on energy consumption and generation.
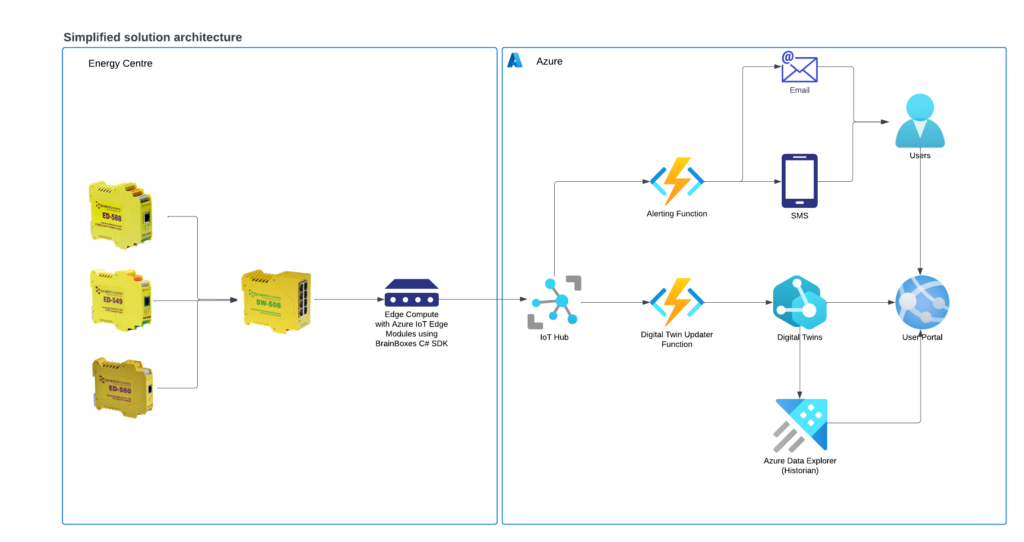
Energy Centre Soluttion Architecture
Further functionality has been built using services such as Azure Data Factory, Azure Event Grid and Azure Functions, enabling real-time alerting via SMS and email, batch reports, and the bespoke portal that wraps all of the functionality together and provides a central place for reporting and administration by both On-Site Energy and their clients.
“Intelligent Industries have built digital twins of all of the assets, and Brainboxes was one of the enablers for us to do that.” – James Brand, Director at Intelligent Industries
By using Brainboxes Remote IO and Ethernet Switch modules, Intelligent Industries provided On-Site Energy with a solution for monitoring and managing the energy centre. Addressing the challenges of production demand, Brainboxes modules integrated with Azure IoT Hub to create a cost-effective and economical smart system for optimising energy generation and distribution on-site.