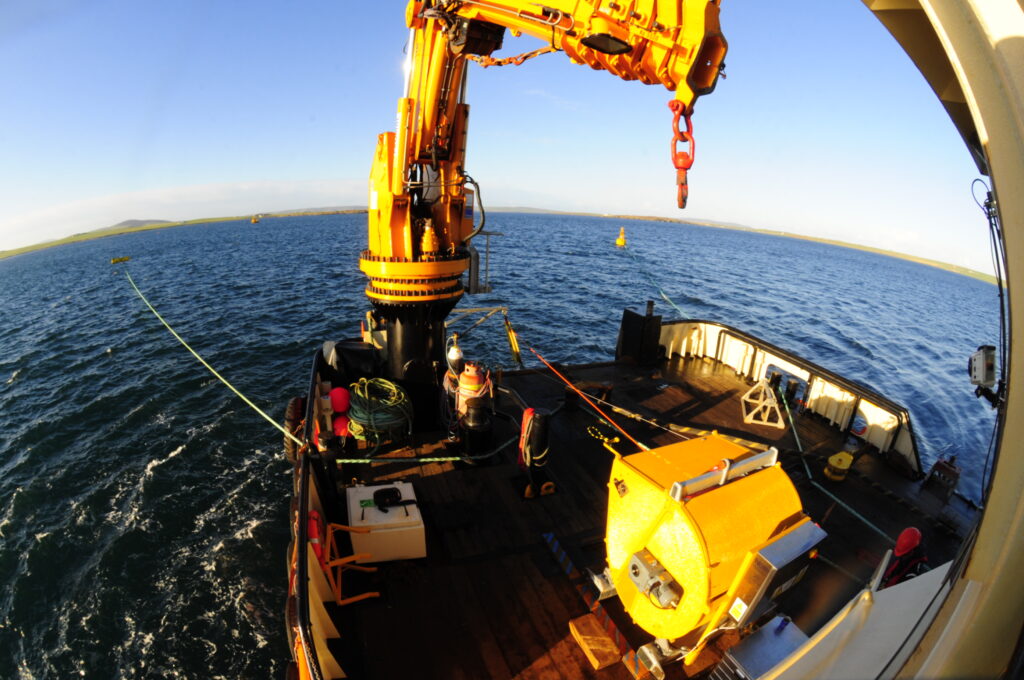
Credit – North Sea Systems
Subsea cables are crucial to the world of modern inter-connectivity and carry vital telecommunications signals, including 99% of the worlds internet traffic, across the globe. Therefore, it’s vital that installed subsea cables are accurately mapped to carry the data. By monitoring the installation of the cables, operators can quickly observe any changes or breaks in the intercontinental communications system.
North Sea Systems is dedicated to developing and operating systems for extreme marine environments. Dave Rigg, the founder of North Sea Systems, is keen to support the marine renewables industry through innovative design solutions. ROVs (remotely operated vehicles) are manoeuvrable underwater and can be used to explore ocean depths, however, ROVs are complex and expensive to operate, and the limited remote-control range doesn’t allow for precision.
North Sea Systems developed Cablefish, a tool that monitors the installation of subsea cables in shallow or high flow environments. The Cablefish system consists of a mechanical carriage, a fibre optic umbilical and an electrically driven winch. Within the carriage, there is an electrical enclosure containing two cameras and lights. The electrical enclosure also contains an altimeter to control the height of the carriage above the seabed, a depth sensor to measure the depth below the sea surface, a roll and pitch sensor, a sonar system and a USBL beacon.
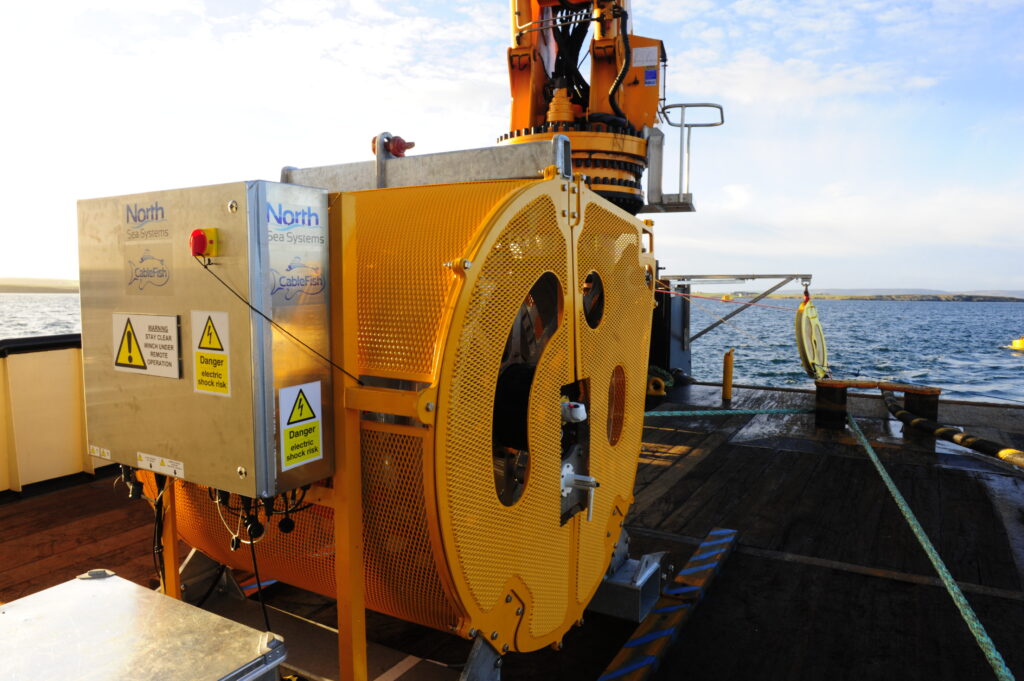
Credit – North Sea Systems
Brainboxes Ethernet switches in the winch cabinet on the surface and in subsea pods enable connection to the Cablefish network, and support the successful operation of the mission-critical equipment. The Brainboxes reliably receive Ethernet data from the video cameras and sensors, and in more murky conditions, they can also receive data from sonar, allowing operators to monitor altitude, depth, live video and sonar.
The system also monitors the roll and pitch to keep track of the performance of the motor of the carriage and umbilical tension. This data is transmitted up to the fibre optic umbilical cable, which runs the telecommunication signals, meaning North Sea Systems aren’t limited by running shorter spans of Ethernet cable.
“There is a job in Taiwan starting in May, another job going out in the States and another one in the North Sea, so it’s really important that the kit is reliable” – Dave Rigg, Founder of North Sea Systems
The Ethernet switches enable the system to be controlled and monitored via a PC over an Ethernet connection or a wireless tablet on the Cablefish network. This procedure provides the operators with GPS coordinates of the cable touchdown point. Additionally, continuous video recordings of the cables enable the operators to visually monitor the product landing on the seabed in real-time. The video recording also helps contractors show their clients that they’ve correctly installed the subsea cables. This leads to less downtime because operators can clearly observe any faults with the subsea cables and quickly jump into action.
Once deployed, switches allow the system to be operated in automated mode, programmed so that the carriage automatically maintains a set position relative to the seabed. Therefore, during operation only a single crew member is required to monitor the system, reducing the manning costs required for 24-hour operations.
“You can’t send a man in a van to go and buy a new bit; you’ve got to deploy with everything you need” – Dave Rigg, Founder of North Sea Systems
The trusted reliability and availability of Brainboxes devices, means North Sea Systems can continuously deploy their systems offshore without the challenging need to constantly find new parts. If the switches fail, the operators will not be provided with any data, causing the whole operation to stop. Therefore, it’s vital that North Sea Systems select a product that is proven to be reliable and robust for working in extreme environments.