Contents
The dawn of the Chips Act means that many new semiconductor fabrication plants (fabs) are being built across the USA and beyond. As chips (integrated circuits) get smaller and smaller, these fabs are of increasing complexity. Critical to reliable chip production is wafer processing, and specifically monitoring and controlling the flow of the gases used in the reactions that turn the silicon wafers into chips. See how Pivotal Systems use Brainboxes Pure Embedded Ethernet Switch to enable their gas monitoring and control system to perform optimally in semiconductor fabs.
Importance of Wafer Processing
Wafer processing is a crucial step in semiconductor manufacturing where thin slices of semiconductor material, typically silicon, are transformed into integrated circuits. This process involves multiple stages of depositing, removing, and patterning materials on the wafer surface to create complex electronic components. Wafer processing is essential because it enables the production of increasingly smaller, faster, and more efficient microchips that power our modern electronic devices, from smartphones to supercomputers.
Challenges in Gas Flow Management
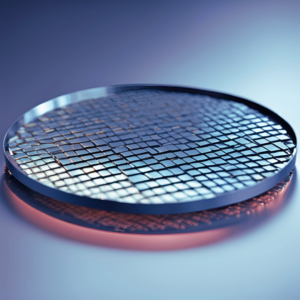
Semiconductor wafer
Wafer processing demands exceptionally precise, consistent, and reproducible gas flow management as semiconductor technology advances. With chip features shrinking to 3 nanometres – roughly the width of 30 hydrogen atoms – even the most advanced mass flow controllers face significant hurdles. These devices must meet exacting standards for accuracy, rapid stabilisation (settling time), and consistent performance (repeatability) to ensure uniform results across all production equipment and maximize the yield of functional chips produced. The challenge is intensified by the need to control minute gas flows, accommodate brief processing windows, and maintain stability during continuous plasma-based manufacturing processes. This level of control is crucial for creating the intricate structures that enable modern electronic devices to be smaller, faster, and more energy-efficient.
The Pivotal Systems and Brainboxes Solution
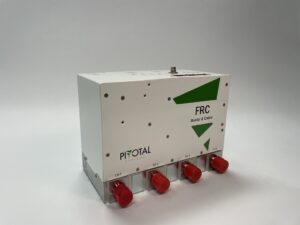
Pivotal System’s Flow Ratio Controller
Pivotal Systems, a leading supplier to the global semiconductor industry, builds advanced Flow Ratio Controllers (FRC) to improve wafer uniformity for manufacturers. This includes providing highly accurate, continuous monitoring and control of the most critical, difficult-to-control parameters in wafer processing today. Controlling the gas flow in semiconductor manufacturing is crucial for effective wafer processing.
Igal Sokolov, Principle Systems Engineer at Pivotal Systems, searched for a compact Ethernet solution. This solution would use Ethernet for real-time communication between five PCB boards inside of the Flow Ratio Controller (FRC). Pivotal Systems considered using various small, embedded switches from off-shore manufacturers. These switches were reasonably priced and maintained the small size that they required. However, these manufacturers couldn’t provide them with the traceability, degree of customer service, or technical support that they needed. Other compact, embedded switches had expensive price tags.
“The price of other switches was prohibitive, and for the mass market it would be too much” – Igal Sokolov, Principle Systems Engineer at Pivotal Systems
This search identified a gap in the market for a solution that balanced size, affordability, and dependable support. To fill this gap, Brainboxes developed the Brainboxes Pure Embedded Switch (PE-505), which offered Pivotal Systems a small, ready-to-use solution that sailed through reliability testing at an economical price. Using a board-to-cable connection to connect Brainboxes Pure Embedded Switch (PE-505) to the Flow Ratio Controller (FRC), all of the data was transferred between the valves and the main controller.
With its mega-compact form, which is smaller than a standard business card, the PE-505 resolves Pivotal System’s challenge of fitting all of the connectivity they need into the small space required for their system. The Pure Embedded switch seamlessly integrated into their system due to the connectors being much smaller than traditional connectors. This design ensures that Pivotal Systems can maximise space efficiency without compromising on Ethernet connectivity. And unlike commercial products Brainboxes guarantees that the PE-505 will be available for a minimum of 10 years; essential for industrial applications.
“First, we looked for some standard solutions, but they were for commercial areas. They were all large, with big MagJacks, RJ45 connectors, and cables that occupied tonnes of space.” – Igal Sokolov, Principle Systems Engineer at Pivotal Systems
The reliability of the Pure Embedded Switch also allowed Pivotal Systems to comfortably integrate industrial communications into their system. To test reliability, the PE-505 was tested using ovens and was power cycled 113,000 times and was proven to be ultra reliable, providing Pivotal Systems with a reliable and reputable supply chain source.
“We knew that the product had to pass the oven test. We checked the connection again and again, and it works!” – Igal Sokolov, Principle Systems Engineer at Pivotal Systems
Overall, using Brainboxes Pure Embedded Switch allowed Pivotal Systems to provide customers with a high-speed, accurate, and reliable flow control solution. This resolved the challenges of regulating system-critical parameters within wafer production.
The PE-505’s potential in the industrial automation sector is demonstrated by its performance in the Pivotal Systems application. Miniaturisation of control systems in space-constrained environments is made possible by this solution, which supports the trend towards more compact and efficient industrial equipment. It also provides an affordable way to integrate Ethernet connection into a variety of devices and enables fast, dependable communication in crucial production processes.